打ち抜き加工|型の使い分け解説(トムソン・ピナクル・彫刻・プレス金型)
打ち抜き加工には、トムソン型、ピナクル型、彫刻型、プレス金型といった異なる型での工法が存在し、
それぞれに特有の特徴や用途があります。この記事ではこれらの違いを詳しく説明します。
打ち抜き型の特徴比較
▶︎ 材厚×寸法精度(公差)
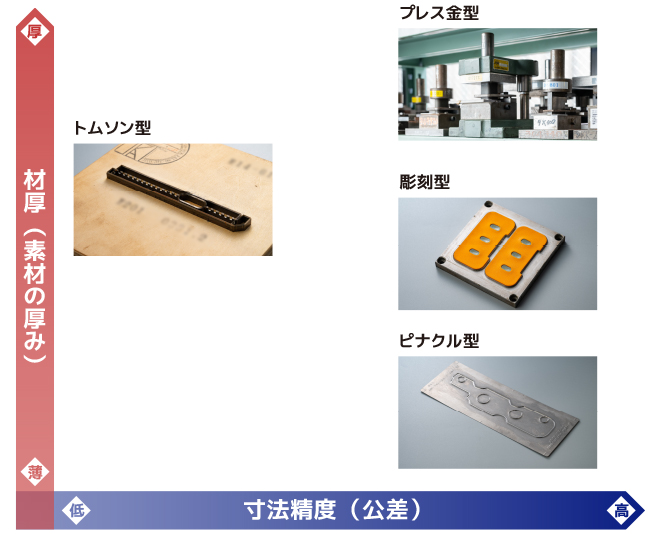
▶︎ イニシャル(初期費用)×リードタイム(金型納期)
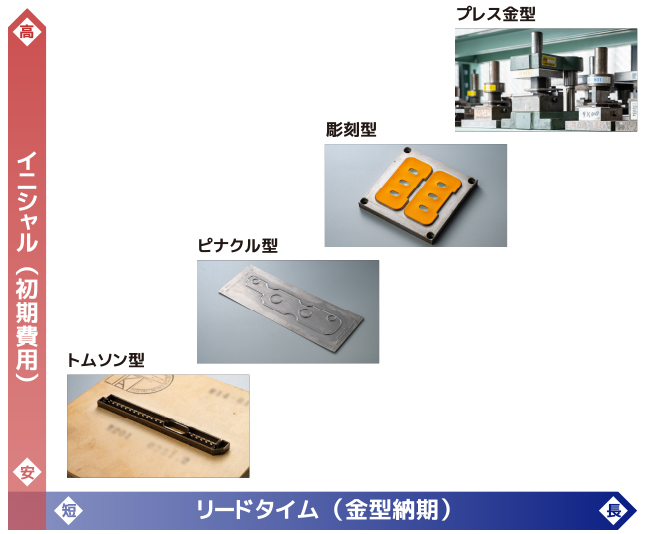
▶︎ イニシャルコスト(初期費用)×ライフ(耐久性)
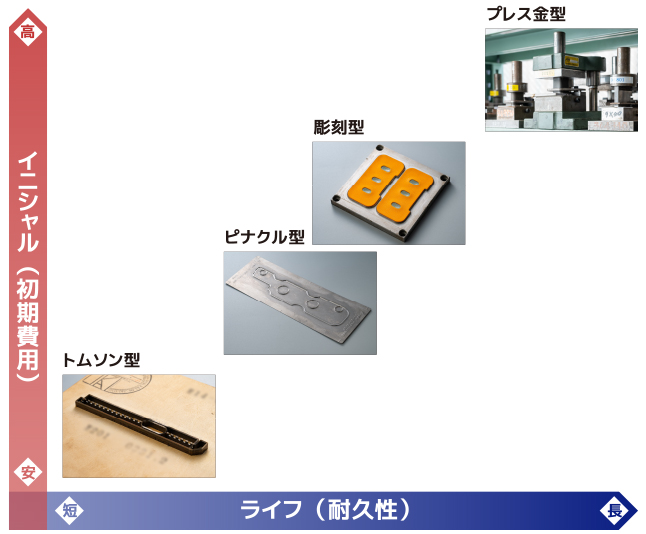
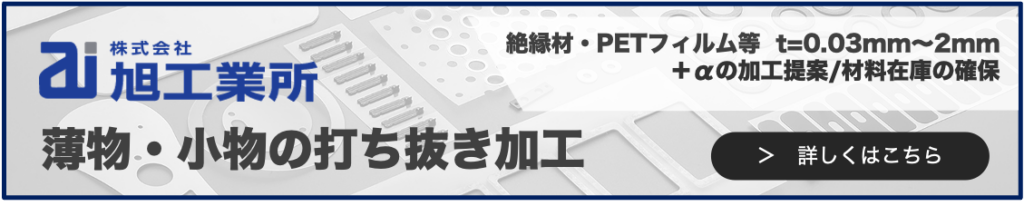
1. トムソン型
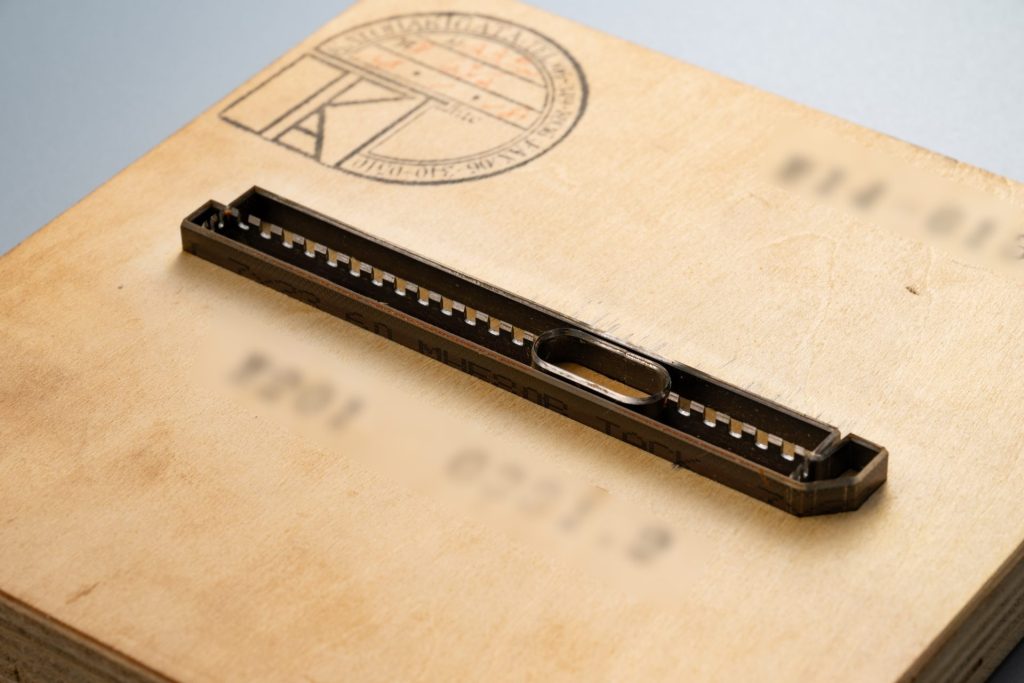
トムソン型(ビク型・木型)とは、ベースであるベニヤ板や樹脂板にレーザーで溝加工を施し、その溝と同じ形状に曲げた鋼の刃物(トムソン刃)を埋め込んだ型です。この型はプレス機で圧力をかけてクッキーの型抜きに似た手法で素材を打ち抜きます。厚い・硬い材質の加工には不向きで、鋭角や細かい形状の再現が難しいというデメリットもあります。
トムソン型のコスト
材料費が安く加工工程が比較的シンプルであるため、初期費用は低めに抑えられます。製作期間も短く、少量生産や試作にも適していることから、短納期を求められる案件で活用されることが多いです。一方で、耐久性の面では金属型に比べると劣る場合もありますが、それを補うほどのコストパフォーマンスの良さが特徴といえます。小ロットから中ロットの生産や試作段階など、短納期や費用を抑えたい場面で重宝されます。
トムソン型の用途
紙、段ボール、樹脂シート、ゴムシートなど、比較的薄い素材の打ち抜き加工に広く用いられます。包装材やラベル、パッケージなどの複雑な形状にも対応しやすく、サンプルや試作品を素早く作りたい場合にも向いています。
2. ピナクル型
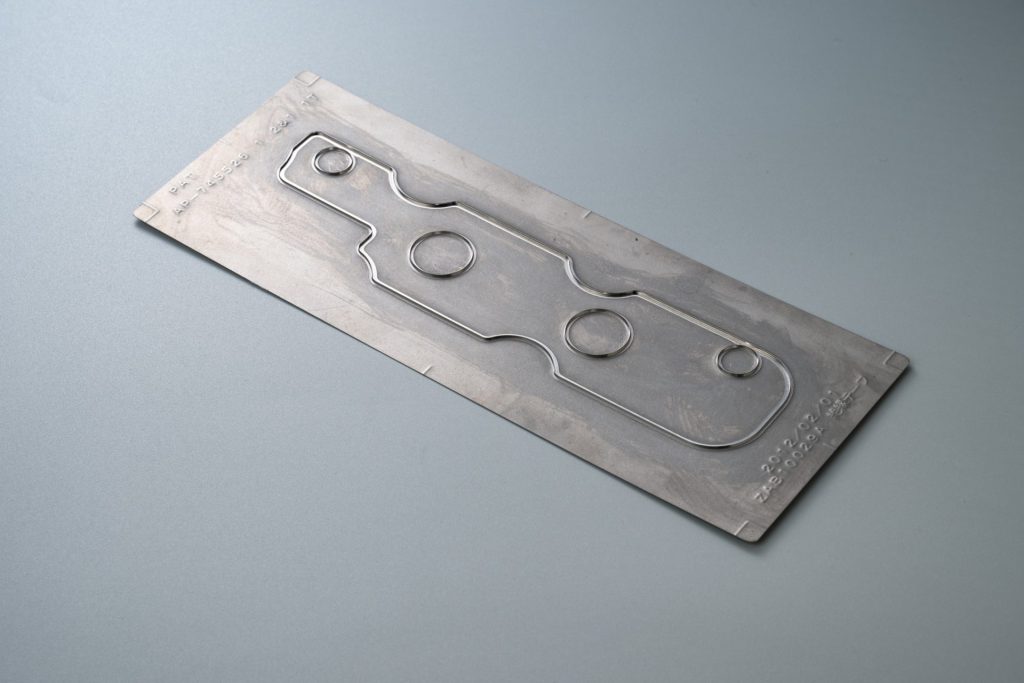
ピナクル型は、金属板に刃として残す部分にマーキングを施し、マーキングをしていない部分を先に腐食させて取り除き、残った凸部分に最後に刃付けをしてできあがります。トムソン型と比較して、金属ベース及び機械加工により抜群の高精度です。刃のつなぎ目がないため、段差のない滑らかな仕上がりが得られます。
ピナクル型のコスト
高品質な刃を使用する分、初期費用はやや高めになります。しかしながら長期的に見ると刃の交換頻度が下がり、トータルの運用コストを抑制できる可能性があります。特に、品質面を重視する案件や、中ロット以上の生産を行う場合には、結果としてコストメリットが得られることが多い型です。
ピナクル型の用途
トムソン型と同様に、紙・段ボール・樹脂などの薄物の打ち抜きに用いられることが多いです。ただし、一般的なトムソン型よりも刃の性能が高いため、やや厚めの素材や高精度の加工が必要な場合に適しています。
3. 彫刻型
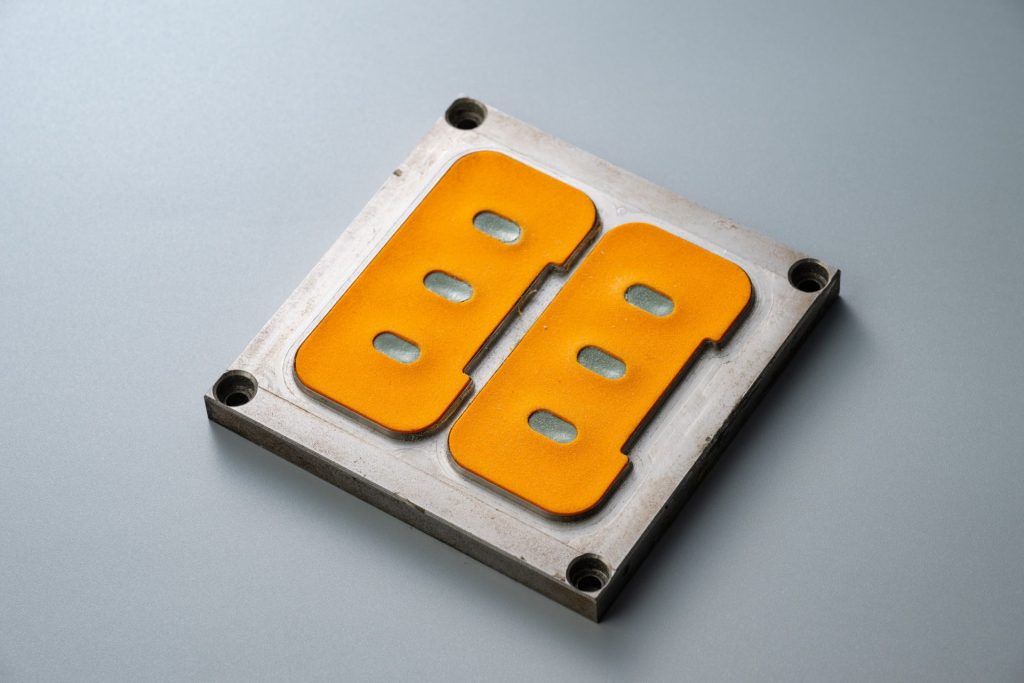
彫刻型は、金属の塊から削り出して作成される刃型で、非常に高い精度を持ちます。刃と型が一体化しており、非常に高精度な加工が可能です。
また、ベースとなる型内部をくり抜くことで、リング形状の内径など不要な部分を刃型内部を通し除去することができて作業工程の削減に寄与することができます。
彫刻型のコスト
初期費用はトムソン型やピナクル型に比べるとかなり高くなるケースが多いです。しかし、金属ブロックから削り出された型は耐久性が高く、頻繁なメンテナンスや部品交換を要しないことから、長期間にわたって安定した品質の製品を生産できます。大ロット生産や高い精度・複雑な形状が要求される製品には適していますが、少量生産や試作段階での導入にはコスト面でハードルが高いといえます。
彫刻型の用途
主に細かいディテールの再現や三次元的な形状、エンボス加工などを必要とする場合に利用されることが多いです。パッケージの装飾や複雑な凹凸を伴う成形品など、高付加価値製品の加工に適していると言えます。
4. プレス金型
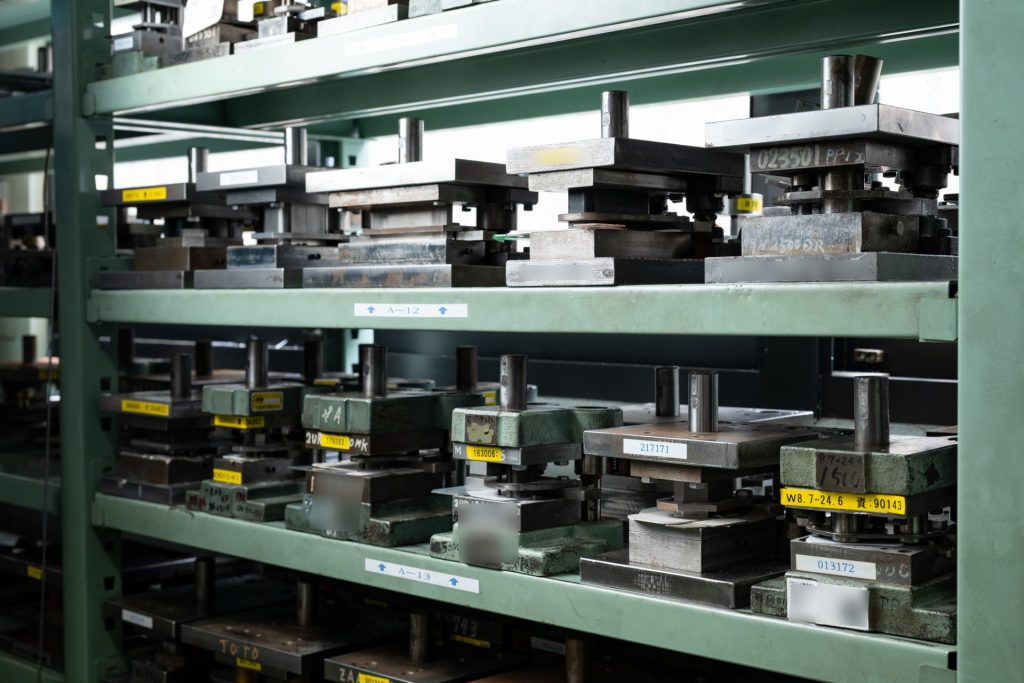
プレス金型は、上型(パンチ)と下型(ダイス)の対で構成され非常に高い精度を持ちます。
プレス金型のコスト
プレス金型は、主に金属部品の大量生産を前提として設計されるため、型そのものが頑丈かつ精密に作られています。そのため、4種類の中では最もコストが高額になりやすいです。製作に高度な技術と大規模な設備が必要であることから、初期投資は非常に大きくなる傾向にあります。しかし、一度プレス金型を導入してしまえば、同一精度の製品を成形できるため、大ロット生産時には大きなコストメリットを生み出せる点が魅力です。製造ラインに自動化装置を導入しやすいという特性も相まって、長期的には一製品あたりのコストを大幅に下げられる可能性があります。ただし、少量生産や頻繁な設計変更には向きにくいため、その点を考慮して検討する必要があります。
プレス金型の用途
自動車や家電製品など、金属部品の大量生産が想定される分野で頻繁に使われます。素材の薄さも問わず、安定した品質で量産可能です。
打ち抜き加工においてよく見られる不良とその原因
バリの発生
打ち抜き加工の際に材料の切断面に残る鋭い突起や余分な金属をバリと呼びます。この不良は、パンチとダイの間のクリアランスが大きすぎる場合に特に発生しやすく、また刃物の摩耗により切断面が不均一になることでも生じやすくなります。適切なクリアランス管理と定期的な刃物のメンテナンスが、バリ発生の防止に重要な役割を果たします。
打痕の形成
パンチが材料に接触した際に生じる凹みや傷を打痕と呼びます。この不良は、主に材料の厚さや硬さが均一でない場合に発生しやすい特徴があります。また、プレス機の設定不良やメンテナンス不足などの機械的な問題も、打痕形成の原因となることがあります。材料の品質管理と機械の定期的な点検が重要です。
形状不良の発生
打ち抜き加工された製品の形状が設計通りにならない状態を形状不良と呼びます。この不良は、型が正しく設置されていない場合に起こるずれや、加工中の材料変形によって引き起こされることがあります。精密な型の設置と材料の適切な固定が、形状不良の防止には欠かせません。
穴あけ不良の課題
穴あけ工程において、穴の位置やサイズが不正確になることを穴あけ不良と呼びます。この不良は、パンチの摩耗による寸法変化や、材料が正しく固定されていないことによる位置ずれが主な原因となります。定期的なパンチの点検と交換、そして確実な材料固定が重要な対策となります。
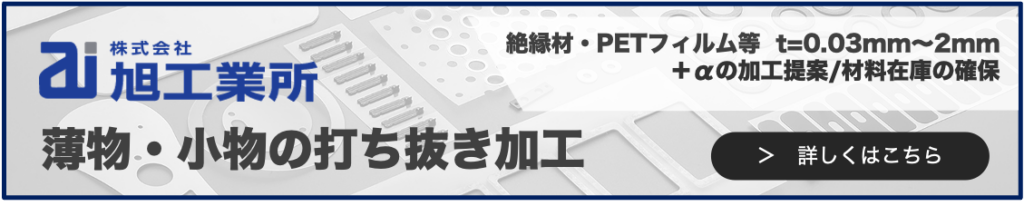
打ち抜き加工時に検討すべきこと
材料選定と仕様の明確化
紙や樹脂シート、金属箔など、どのような素材を使用するかによって加工方法や必要な設備、コストが変わります。素材の厚さや硬さ、柔軟性なども合わせて確認すると安心です。また、製品がどのように使われるのか(例:包装材、工業部品、装飾用など)を共有することで、適切な材料や加工条件の選定につながります。
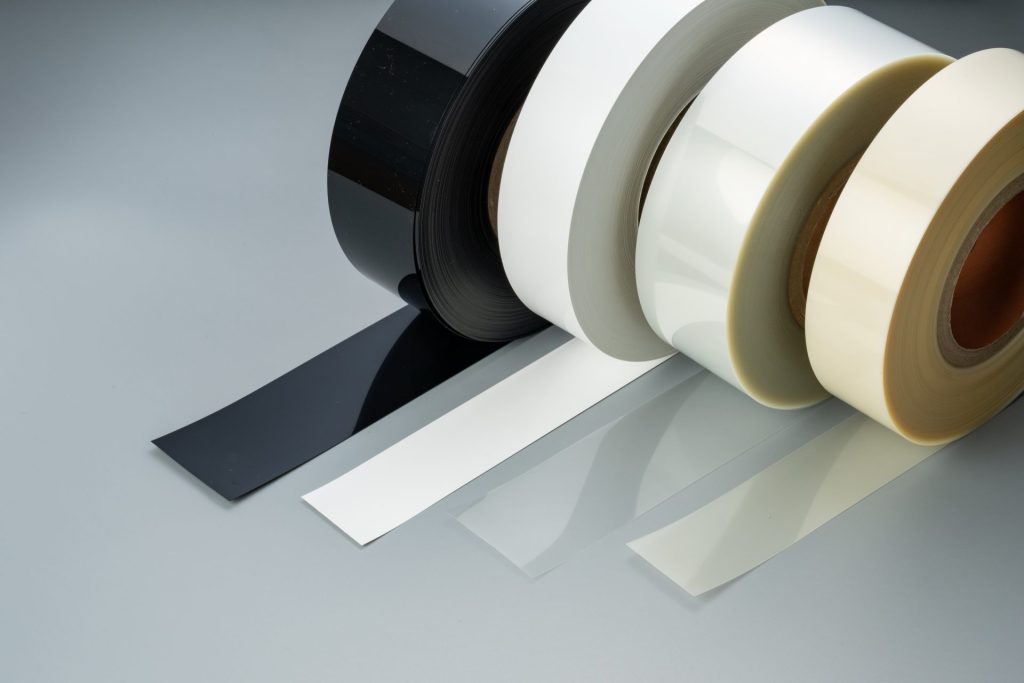
加工形状・難易度の把握
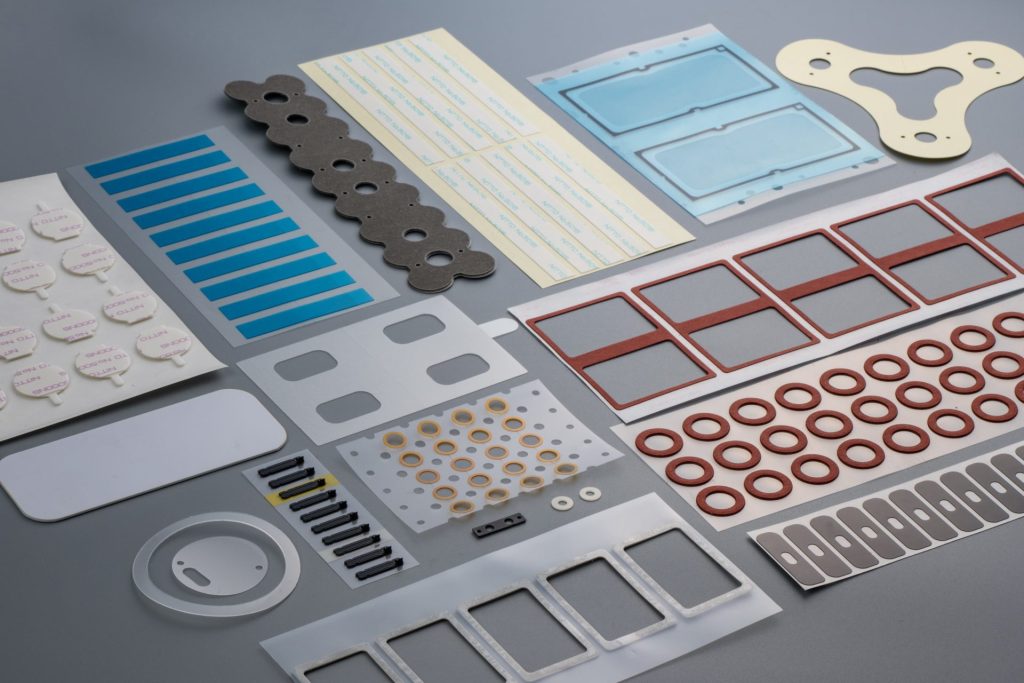
角が多い形状や細かい穴あけが必要な場合は、加工難易度が上がります。場合によっては追加の型加工や工夫が必要となるため、形状データを共有し、実現可能性を確認しましょう。刃型の構造上、極端に細いパーツや急激なカーブなどは再現が難しい場合があります。加工作業者やメーカーと相談し、デザイン修正が必要かどうかを確認することをおすすめします。
コスト
同じ形状でも、トムソン型やプレス金型など選ぶ型の種類によって初期費用や単価が大きく変わります。生産量や品質要件に合わせてベストな方法を選ぶことが重要です。
試作・サンプル確認
初めての形状や材質で加工をする場合は、試作やサンプル品を取り寄せて実際の品質を確認するとトラブルを防ぎやすくなります。
※サンプル打ち抜きのご相談はこちら
打ち抜き加工における生産向上への取り組み
金型の最適化
定期的な金型の点検とメンテナンスを行うことで、摩耗を防ぎ、長期間にわたって安定した加工が可能になります。金型の寿命を延ばすことで、交換頻度を減らし、コスト削減にもつながります。また、プレス金型においてはパンチとダイのクリアランスを適切に設定することで、バリやダレを最小限に抑え、加工精度を向上させることができます。これにより、良品率が上がり、再加工の手間が減少します
打ち抜きプロセス・配列の改善
刃物の切れムラは加工品質に大きな影響を与えます。また、その調整時には機械を停止する必要があるため、生産性低下の要因の一つとなっています。
また、一度に打ち抜く型の配列も重要な要素となります。規定の材料から最も数多く、あるいは効率よく打ち抜けるよう配列を確認することが重要です。これらを見直すことで歩留まりの改善が期待できます。
動画で見る打ち抜き工程
ファイバー紙の打ち抜き ※2倍速再生、音声なし
絶縁フィルムの打ち抜き ※音声なし
薄物・小物の打ち抜き加工はお任せください!
薄物・小物の打ち抜き加工は旭工業所へお任せください。
70年以上のノウハウを活かし、お客様のご希望の仕様へと仕上げます。多層複合材の打ち抜きや、使用時に作業性を向上するためのタブ付け・色付けの加工などにも対応いたします。
「こんなものは打ち抜けないか」と、お気軽にご相談ください。
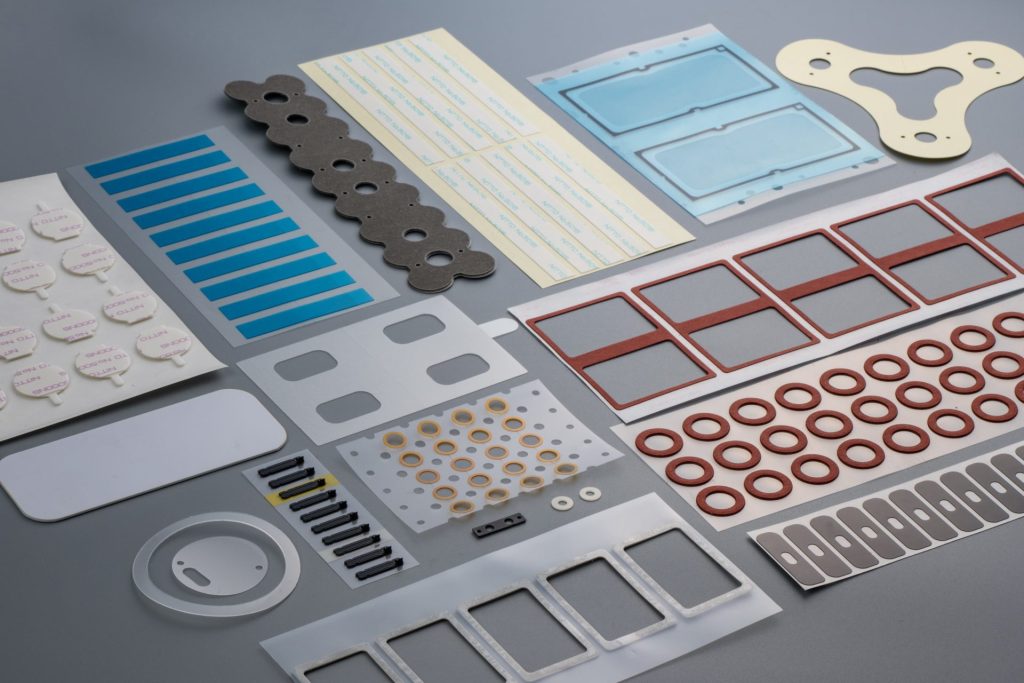
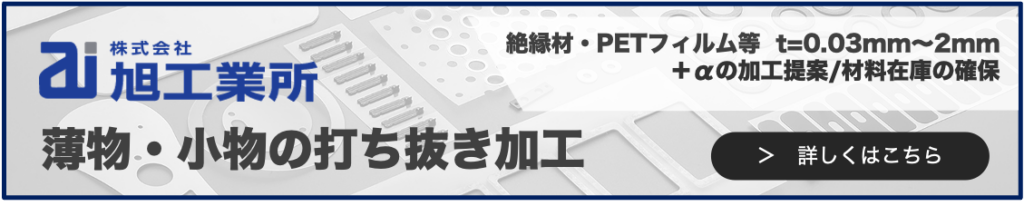